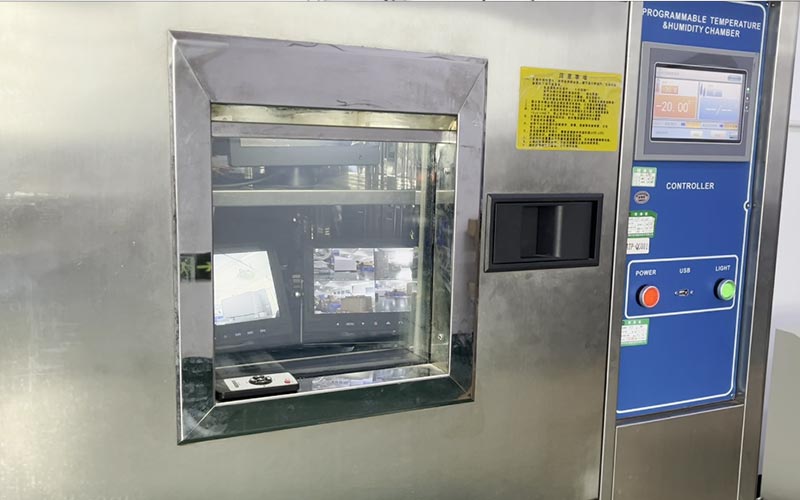
In the field of large vehicle safety, on-board cameras play a vital role in providing drivers with critical visual information to enhance driving safety. However, these cameras not only need to cope with normal driving environments, but must also operate robustly in extreme weather and harsh conditions. To ensure that large vehicle cameras perform as expected in extreme environments, a series of specialised tests such as waterproofing, high temperature, low temperature and vibration are essential. By examining the purpose and process of these tests, we can better understand their importance in enhancing the reliability and safety of vehicle systems.
Table of Contents
Waterproof Performance Testing
The waterproof test is designed to verify the waterproof performance of the vehicle camera’s housing and sealing structure. During the test, the camera is first sprayed with liquid using a dosed water jet or a spraying device that simulates rain. Subsequently, the camera is immersed in water to simulate the extremes that may be encountered in adverse weather conditions. Such testing not only assesses the water resistance of the housing, but also verifies the performance of the seals to ensure that the internal components of the camera are protected from moisture.
High and low temperature tests (-20°c – 70°c)
High and low temperature tests examine the performance of the camera under high and low temperature conditions, respectively. High-temperature tests are usually conducted in a thermostatic chamber, where the camera is placed in a hot environment to simulate actual use in the hot summer or under the scorching sun. The low-temperature test, also conducted in a thermostat, exposes the camera to extreme cold conditions to simulate use in a cold winter or in the Arctic. These two tests evaluate the response of the camera’s internal components to temperature changes by simulating the operating environment under different temperatures to ensure that it works stably under all climatic conditions.
Vibration Test
The vibration test is designed to simulate the vibrations and shocks that a vehicle may face during driving. In the test, the camera is mounted on a vibration table and tested under different frequencies and amplitudes of vibration. This assesses whether the camera’s mechanical structure and internal electronics are sufficiently resistant to vibrations during vehicle travel. The vibration tests cover not only vibrations during normal driving, but also shocks in special situations, such as crossing bumpy roads or passing over uneven surfaces.
In our expert discussion of environmental adaptability testing for large vehicle cameras, we gained insight into the significance and process of key tests such as waterproofing, high temperature, low temperature and vibration. These tests are not just about standards compliance, they are about ensuring that large vehicle cameras function as intended in all kinds of harsh conditions, providing reliable visual information to drivers. Through these specialised tests, manufacturers can comprehensively assess the environmental adaptability of cameras and improve their reliability under extreme conditions, thereby enhancing the safety and performance of the entire vehicle system. In the future, as technology continues to evolve, we look forward to witnessing more advanced testing methods and technologies in the large vehicle industry, bringing even more excellence to vehicle safety and driving experience.